Our understanding of good product design and effective construction in an IoT project is our commitment to quality, functionality and state-of-the-art technology. A perfect basis for efficiency and cost savings in the areas of development and production. And thus a further guarantee for tangible competitive advantages. Within the HK.SYSTEMS network, Hoffmann + Krippner GmbH & Co. KG & Co. KG, based in Buchen (Odenwald), takes on this challenging task. It specializes in the development and production of individual HMIs and printed electronics. In interdisciplinary teams, we design and construct IoT devices according to your requirements.
With our full-service package, we cover all areas of product development – from design and engineering to development and production through to the selection and support of suppliers. In short: we deliver an intelligently structured design process that creates optimum functionality and thus added value.
Effective product design
Customer benefits at a glance
- Efficient development and design processes
- Cost-saving production processes
- Independent appearance of the products as part of the IoT project
- Parts production in line with the corporate design
- Project-oriented | Functional | Ergonomic | Sustainable | Aesthetic
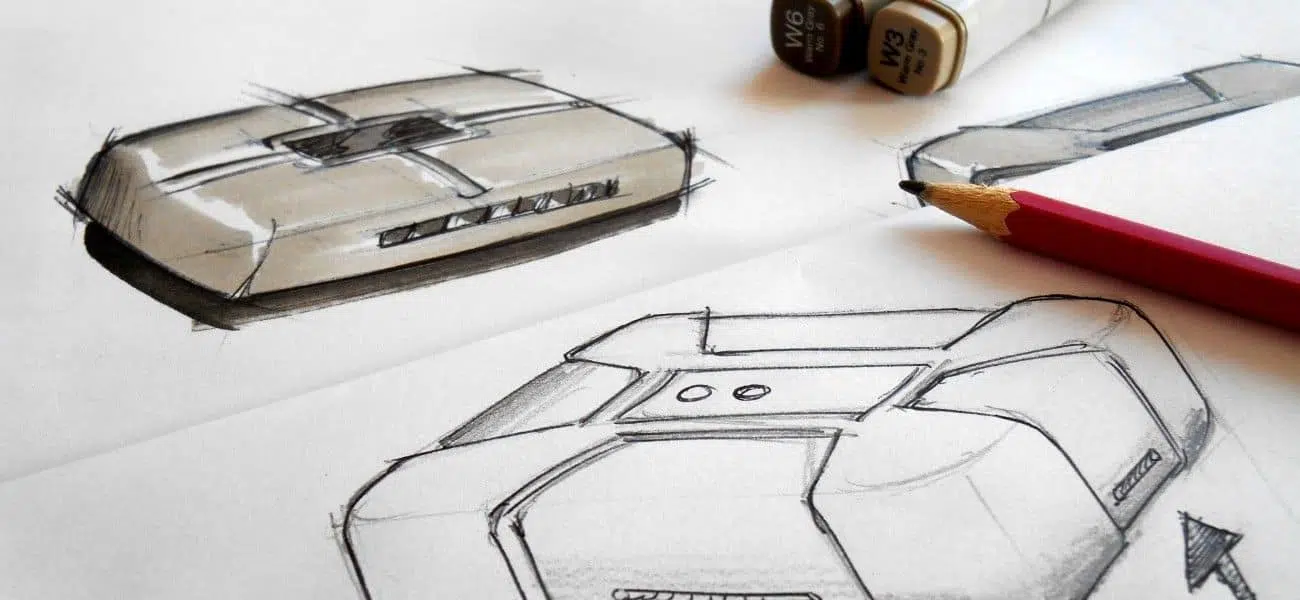
The right technologies and the right resources
Our Design + Construction team at HK.SYSTEMS harmonizes the technical and ergonomic requirements, the material properties and the demands of the necessary certifications with an appealing form that matches the project requirements. To do this, we think about the design of the parts, the assembly and the selection of suitable production technologies.
We know: With the right tool and housing concepts, fast and cost-effective production is possible. We can significantly accelerate the development process using innovative methods such as additive manufacturing technologies. And we then have sufficient resources to produce plastic and metal parts on an industrial scale for the respective IoT project.
The workflow – from idea to product
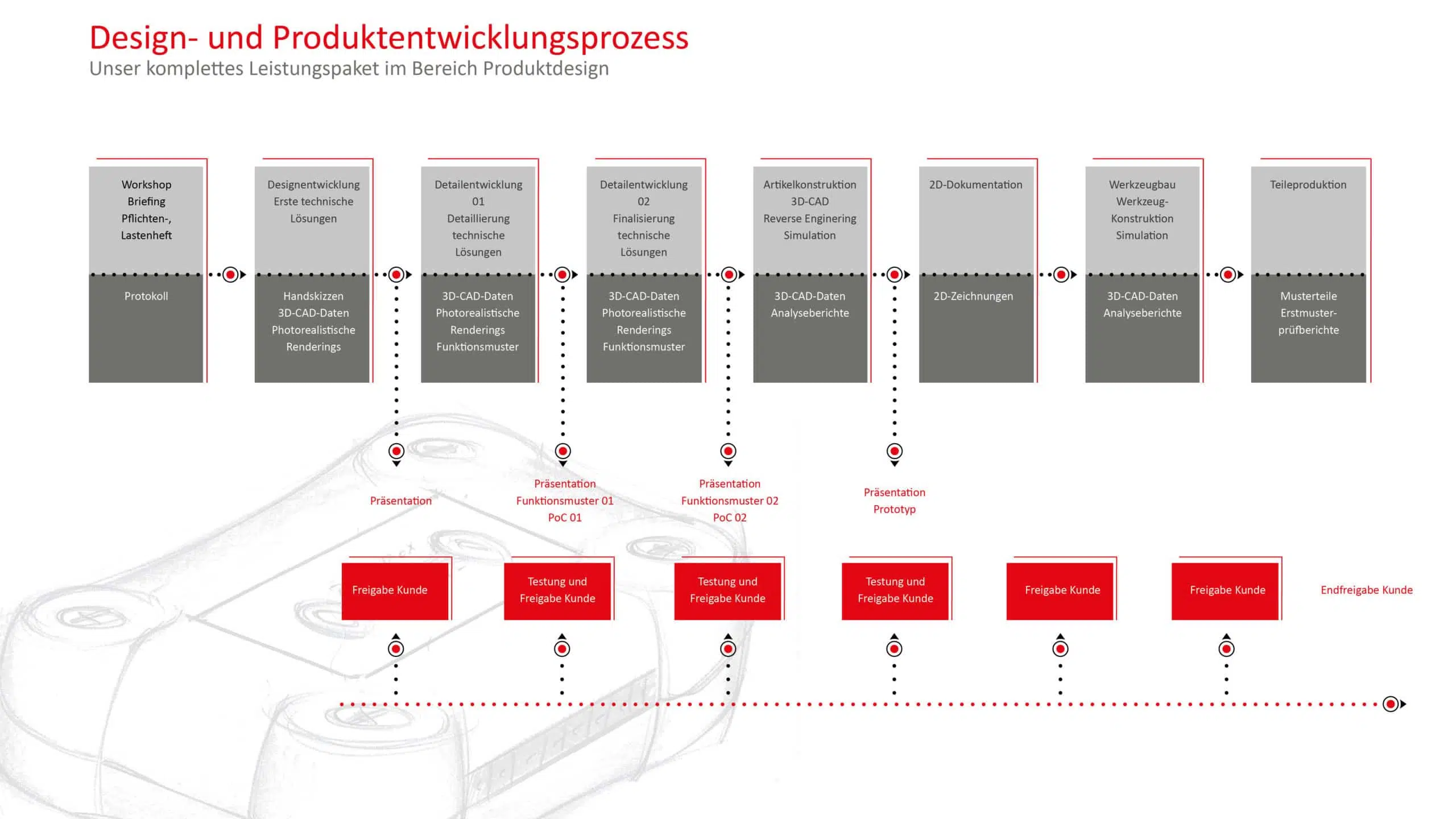
- The first step in a joint workshop is to clarify the detailed requirements. We then work with the customer to develop initial technical solutions and define the next steps.
- Next, we delve into the detailed development of the technical
Solution concepts: from the design detailing of a selected design draft to the integration of existing parts and components and the refinement of selected technical solution approaches. - Next step: The proof of concept (PoC) and the functional samples with the selected additive and other manufacturing processes to test the technical functions.
- This is followed by the technical concept and design development, including the integration of all existing or newly defined parts and components. We develop technology proposals for production and different design variants.
- The next step is the production-ready item design for all components of the assemblies, housings and complete devices. We then realize the prototype construction.
- Our comprehensive expertise in reverse engineering and injection moulding simulation forms the bridge to final production and industrialization: All parts, assemblies, housings and complete devices developed by us are now going into series production. Of course, we also take care of the procurement and production of the necessary series tools and final assembly.
Special know-how: Additive manufacturing
High-quality plastic parts from the 3D printer as an alternative to the tried-and-tested injection molding process: Whether medium or small series or prototypes – we have mastered the innovative additive manufacturing technologies in the 3D printing process and produce high-quality plastic parts: this technology not only saves weight and costs in the long term. You can also react more quickly to changing requirements, order according to the situation and do not have to keep expensive stocks. The advantages of this pioneering technology are obvious:
- Short production time: a few days to prototype
- Sustainability: less material waste
- Customization: quick adaptation of 3D data
- Project acceleration: Short-term + flexible production
- Lightweight structures: a wide range of possibilities
- Cost efficiency: lower tool costs and inexpensive test prints
- Free scalability: complex geometries possible
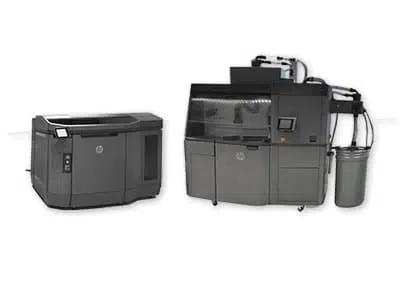